I am a 17 year old living in Canada. I first started forging roughly 2 years ago. One year ago I took a class with the American Blacksmith Brian Brazeal, where I also met Joshua McLaren, and Alec Steele. Since coming back from Mississipi I have been forging in my backyard. At this point I am searching for a dedicated forging space. Daniel Lea has introduced me to this forum.
Now that the intro is done, I can share a recent project of mine.
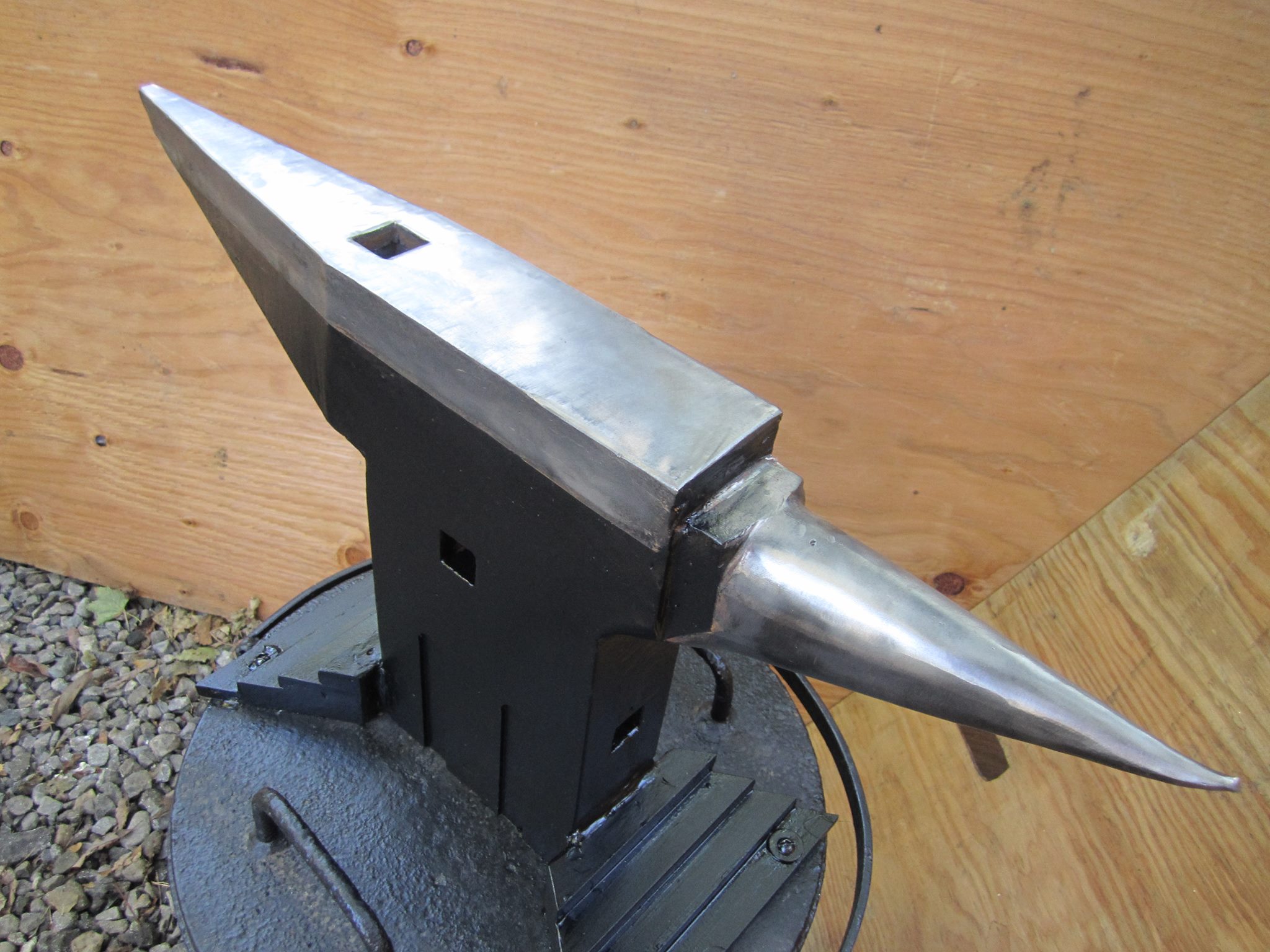
This was a final high school metal shop project which I began in March, and finished in September.
You can read the full writeup I did on Anvilfire through This link
I also made three videos while working on the anvil
First Anvil Making Video
Second Anvil Making Video
Last Anvil Making Video
Thanks for Reading, I look forward to seening the work of others on this forum.